Use cases
An operational excellence manager of a mid-sized company in the industry uses ABCKPI to replace and centralize all Excel and Powerpoints related to continuous improvement management
Situation before using ABCKPI
Un processus de pilotage de l’amélioration continue existant de manière historique
The company has a continuous improvement process led by the operational excellence teams. The process is composed of 4 steps with (i) the collection of data related to indicators (achieved, objectives, rationalization of gaps) and the progress of action plans initiated or simply to be presented to the management review for validation, (ii) the entry of such data, (iii) the realization and animation of the journal as such and (iv) the implementation of corrective measures.
In reality, this company being an international industrial group, the process includes other steps with the transmission of information to the parent company or other, but in this use case we will focus on these four steps.
All of these steps are done in Excel and Powerpoint with some data collected in SAP. Each of the indicator managers works on their own spreadsheets for indicators and action plans (identical formats but multiple Excel files).
excel
The observation : A lot of time and energy wasted in the continuous improvement process.
During our discussions with the operational excellence teams, we identified 7 issues impacting the efficiency and effectiveness of the process :
- The data is not centralized in a single tool : every month, the facilitator has to run around the company to gather the information and multiple errors are made in this manual cross-checking work (different versions, data not updated, etc). A significant amount of time (estimated at half a day per week) and quality information is lost in this step
- Multiple entries are made manually in different tools. Information flows between SAP, Excel and PowerPoint but the work is done manually. It was not possible to evaluate precisely the loss of time in this second step, but 20 employees are concerned by the data entry and they could also lose an average of half a day per month on this work.
- Errors or out-of-date data are often found when facilitating the meeting. This is obviously problematic as everyone starts giving their own number and the meeting becomes inefficient.
- Monthly meetings are focused on management and operational staff do not participate. As a result, there is a poor flow of information between the different levels, both on possible corrective actions and on priority objectives.
- The weekly production meetings have taken the approach of alternating leaders because time is limited; not everyone presents at each occurrence. This allows each manager to have regular time to express the situation of his or her indicators, but it does not necessarily allow to focus on the most urgent ones of the period (week
- Since information is shared in small groups, people who are responsible for an action are not always aware of their necessary involvement in a project.). This slows down projects as soon as they are launched.
- The multiplicity of excel files (20 different files) does not allow a good overview. It is difficult to facilitate the process effectively under these conditions.
- Analysis and comments on a deviation from a goal are not documented, they are simply mentioned orally. Information is quickly lost and it is not easy to capitalize on the history.
- Once an action or action plan is finalized, no impact measurement is performed. The impact of the action on an indicator is not monitored. Yet this is often interesting: What was the gain of the action? Is it necessary to repeat it on another sector? Can we improve this gain on a future action plan? The impact of an action on an indicator is not measured so that no conclusions can be drawn.
Based on these observations, we made the ABCKPI platform available to respond to all the dysfunctions identified in the continuous improvement process.
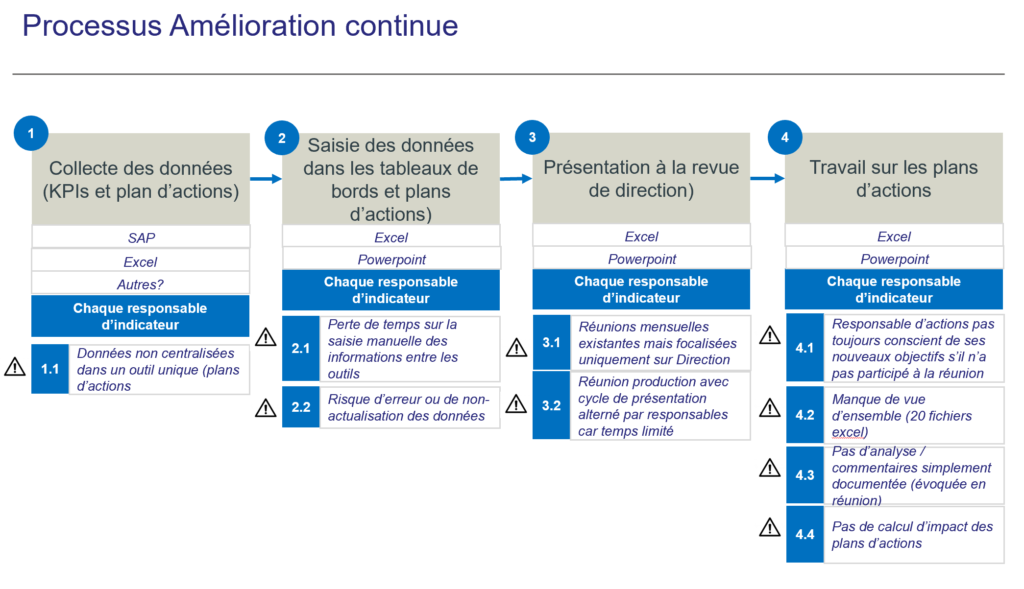
Situation after using ABCKPI
Indicators, objectives and action plans are grouped together in an easy-to-use platform that is accessible to everyone (computer, telephone, etc.).
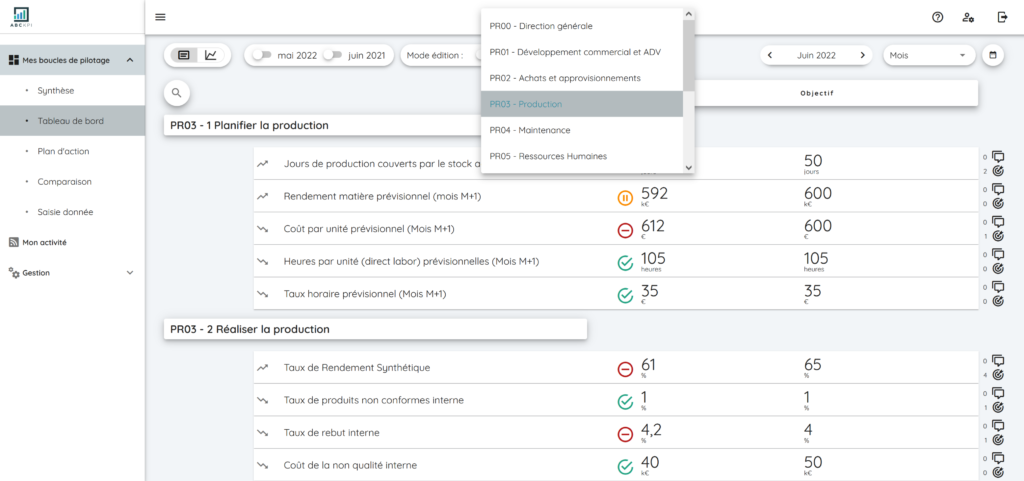
Each process can be defined within a control loop. In this case, we are inside the “PR03 – Production” control loop and we can directly see the achievement and the target for each indicator.
Data can be entered by users, integrated in bulk via excel or integrated automatically via APIs.
On the right of each indicator, it is possible to visualize the action plans that have already been carried out and to create new ones in a few seconds.
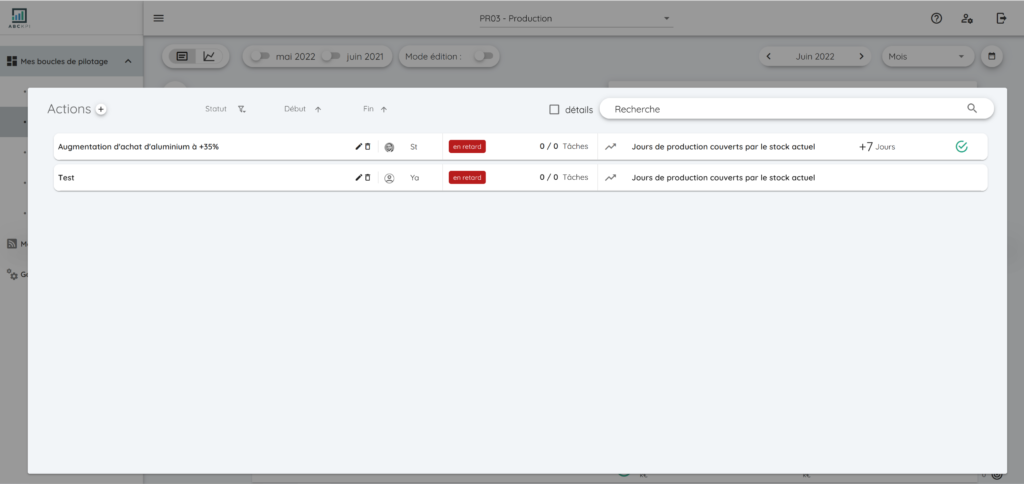
All existing action plans in the control loop can be viewed, filtered and sorted in the action plan page.
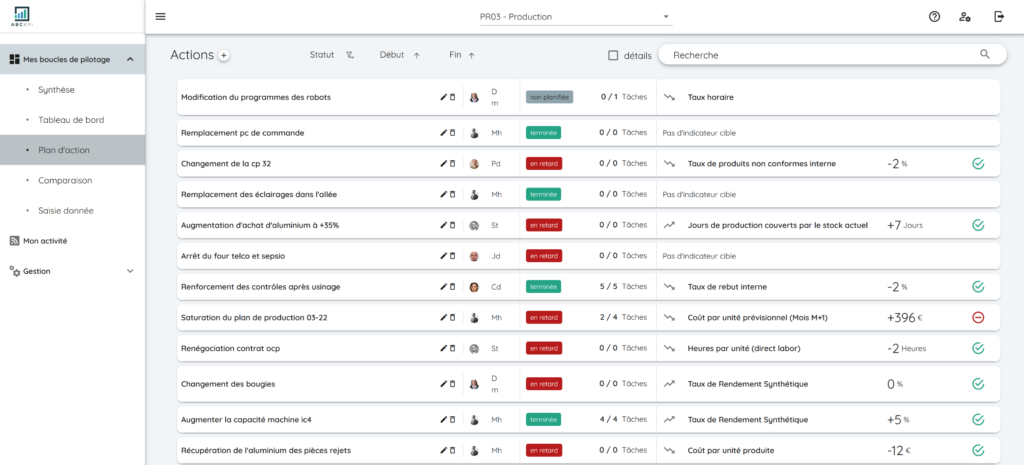
Within each action plan, it is possible to easily monitor the impact of the action plan on the indicator.
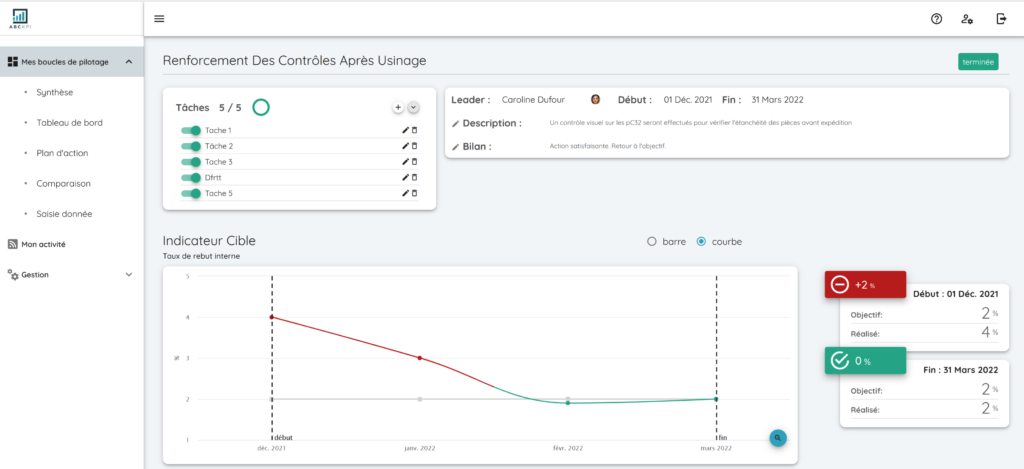
In summary
The company now benefits from a platform where all indicators, objectives and action plans are centralized (see problematic 1.) and depending on the indicator the information can be entered, imported en masse or imported automatically via a script (see problematic) 2.). Concerning the reliability of the data, they are updated directly (depending on the chosen method of updating the information) and there is only one source of information (see problematic) 3.).
Moreover, in terms of communication and exchange, it is much easier to involve different team leaders in the management review thanks to a dematerialized application (see problematic) 4. and 5.) and the persons in charge of actions are notified via the application of the actions they are responsible for (see problematic) 6.). Analyses and comments are documented in the dialog boxes provided for this purpose for each indicator (see problematic 8.).
For the facilitator, it is a real time saver because he no longer needs to chase after all of his 20 managers to obtain his 20 Excel files; the centralization of information provides him with a good overview and a means of steering his process effectively (problematic 7.). In addition, it can measure the impact of an action on an indicator and capitalize on what already exists to identify new actions and new performance gains (problematic 9.).