Use cases
A continuous improvement manager from the automotive industry uses ABCKPI to digitalize his continuous improvement process and his monthly steering meetings.
Situation before using ABCKPI
The creation of an excel tool to track information
With the support of the general manager, the company’s continuous improvement manager has set up a continuous improvement management system validated by IATF obligations (see below for more information on IATF).
Its management system is based on the process approach. It has defined 8 processes: PR01 – General Management, PR02 – Business Development and Sales, PR03 – Purchasing and Supply, PR04 – Production, PR05 – Maintenance, PR06 – Human Resources, PR07 – Finance, PR08 – IT.
For each of these processes, performance indicators and monthly objectives have been defined. For example, the PR04 – Production process is composed of a number of indicators: Synthetic yield rate (%), Non-conforming products rate (%), Cost per unit (€), Hourly rate (€/u), etc.
Each of these processes and indicators are tracked in an excel file with a tab per process. Below is an excerpt from the dashboard for the 4 indicators mentioned above including dummy data.
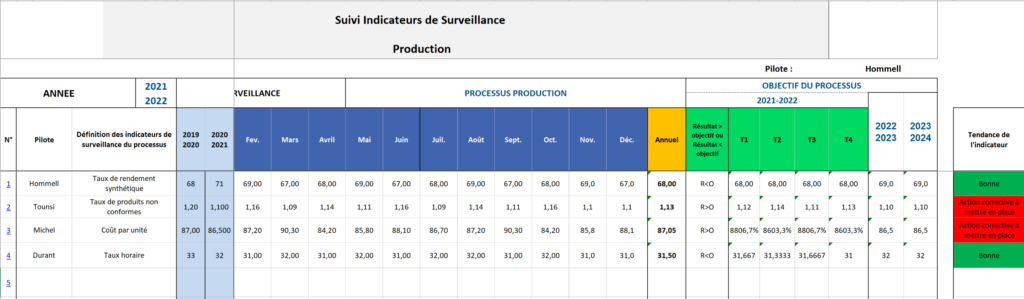
Each indicator has a target and is monitored monthly. When the indicator is not at the target, a corrective action plan is put in place with the aim of returning to the target within a defined period.
The Excel file therefore necessarily includes a tab for each action plan. In the previous example, an action plan should be initiated for the rate of non-conforming products and the cost per unit.

Transposing information into PowerPoint for monthly reviews with the DG
Every month, a performance management meeting is held with the Management Committee and the process managers. Each process manager recalls his objectives, presents his figures and the action plans in progress including the estimated gain on the organization for each action.
Prior to the meeting, follow-ups are made with the various managers to ensure that their information is properly filled out.
To animate the meeting, a powerpoint is used and the data from the excel file is copied into powerpoint.
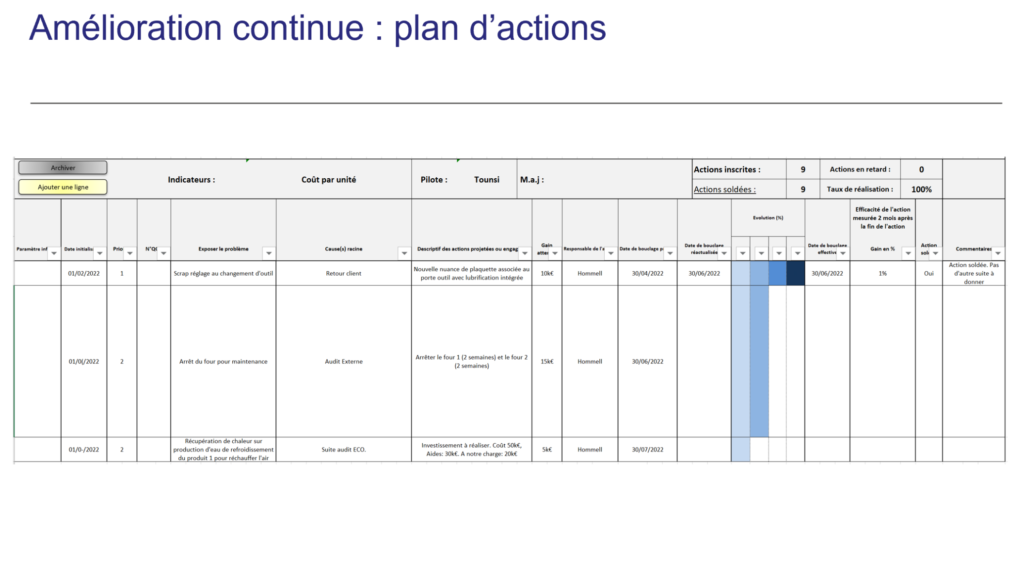
Issues raised
This process is under control and the objective seems to have been reached: continuous improvement is implemented in the company, strategic objectives are broken down into processes, indicators and objectives, action plans are initiated when the results do not meet the objective and follow-up meetings are organized monthly by the Management Committee.
However, the company told us the following points of difficulty:
- The processing time to maintain the excel and powerpoint file is substantial
- Excel and PowerPoint tools are not ergonomic: action plans are difficult to read, formulas have to be updated regularly, and many data have to be calculated manually
- Regular bugs and data loss occur regularly
- Other action plans are regularly deployed in the organization in other Excel files, which complicates the overall readability of the process
- No possibility to easily measure the gain related to the action plan in Excel
- Data not accessible remotely from the phone
Situation after using ABCKPI
Indicators, objectives and action plans are grouped together in an easy-to-use platform that is accessible to everyone (computer, telephone, etc.).
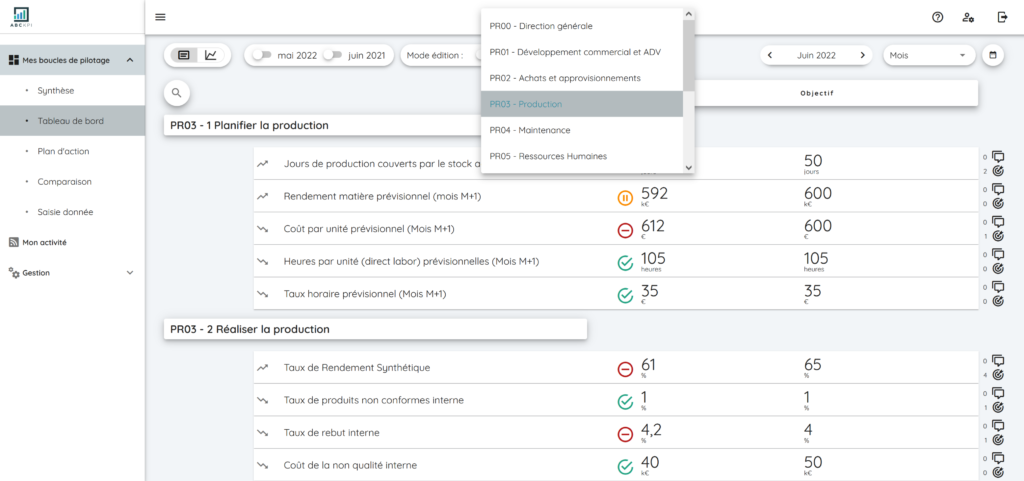
Each process can be defined within a control loop. In this case, we are inside the “PR03 – Production” control loop and we can directly see the achievement and the target for each indicator.
Data can be entered by users, integrated in bulk via excel or integrated automatically via APIs.
On the right of each indicator, it is possible to visualize the action plans that have already been carried out and to create new ones in a few seconds.
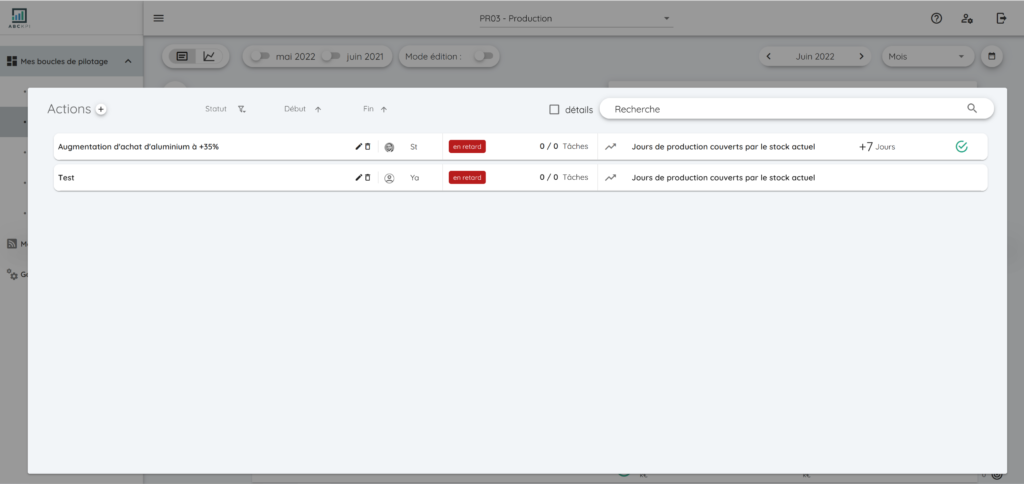
All existing action plans in the control loop can be viewed, filtered and sorted in the action plan page.
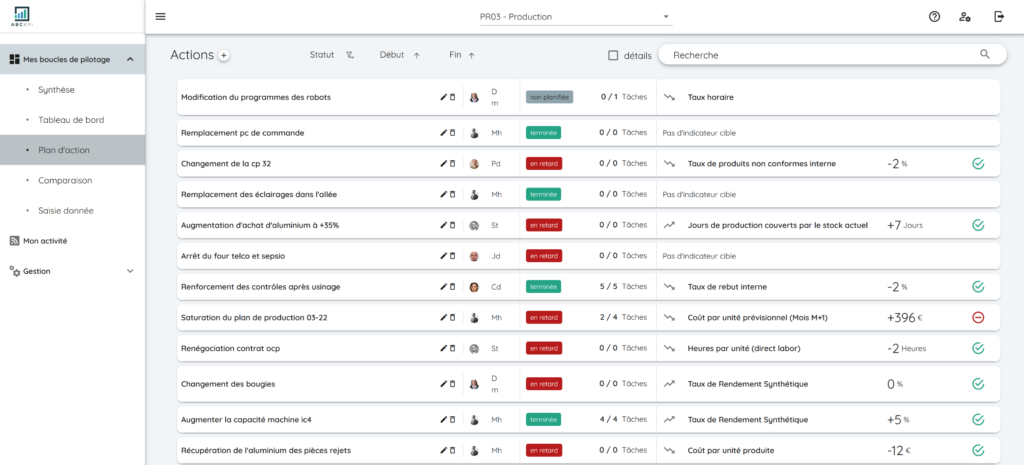
Within each action plan, it is possible to easily monitor the impact of the action plan on the indicator.
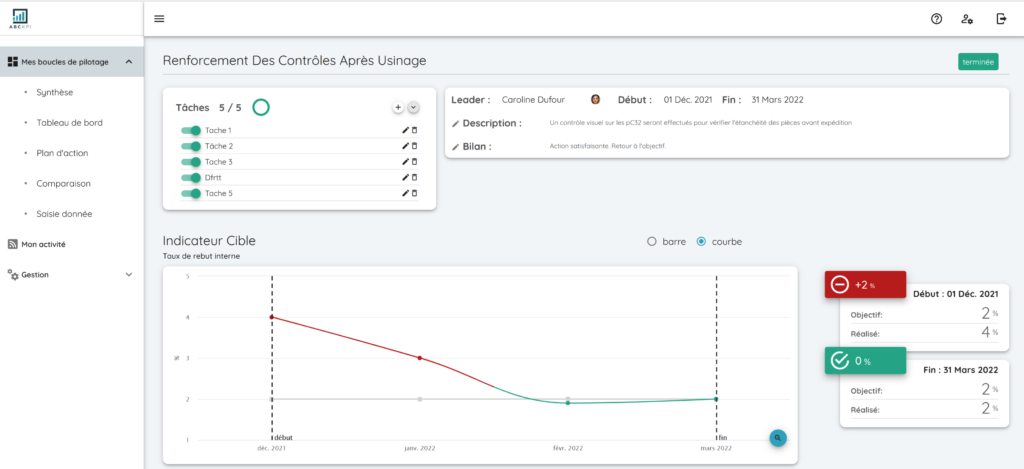
Appendix: IATF 16949: General Key Principles
The IATF (International automotive task force) is a standard that establishes the requirements for a quality management system (QMS). It is specifically focused on the automotive sector. Its primary objective is the development of a quality management system that provides for the implementation of continuous improvement, focusing on the prevention of defects and the reduction of variations and waste.
Companies applying for IATF 16949 certification hope to be registered as a supplier by meeting the criteria of a QMS dedicated to the automotive sector. More than 65,000 suppliers worldwide are currently certified to ISO/TS 16949 and all requirements of IATF 16949 are applicable: The requirements are generic and are intended to apply to any supplier working on automotive-related design, development, assembly production, machining, installation and service processes.
The standard is based on seven quality management principles including management/employee motivation and involvement, process approach and continuous improvement.
These quality management principles are defined as follows:
- Customer orientation
- Leadership
- Involvement of employees
- Process approach
- Improvement
- Fact and data-based decision making
- Managing mutually beneficial relationships
Links :
https://www.iatfglobaloversight.org/
https://en.wikipedia.org/wiki/International_Automotive_Task_Force